
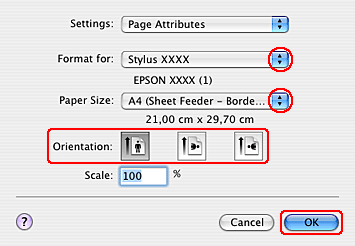
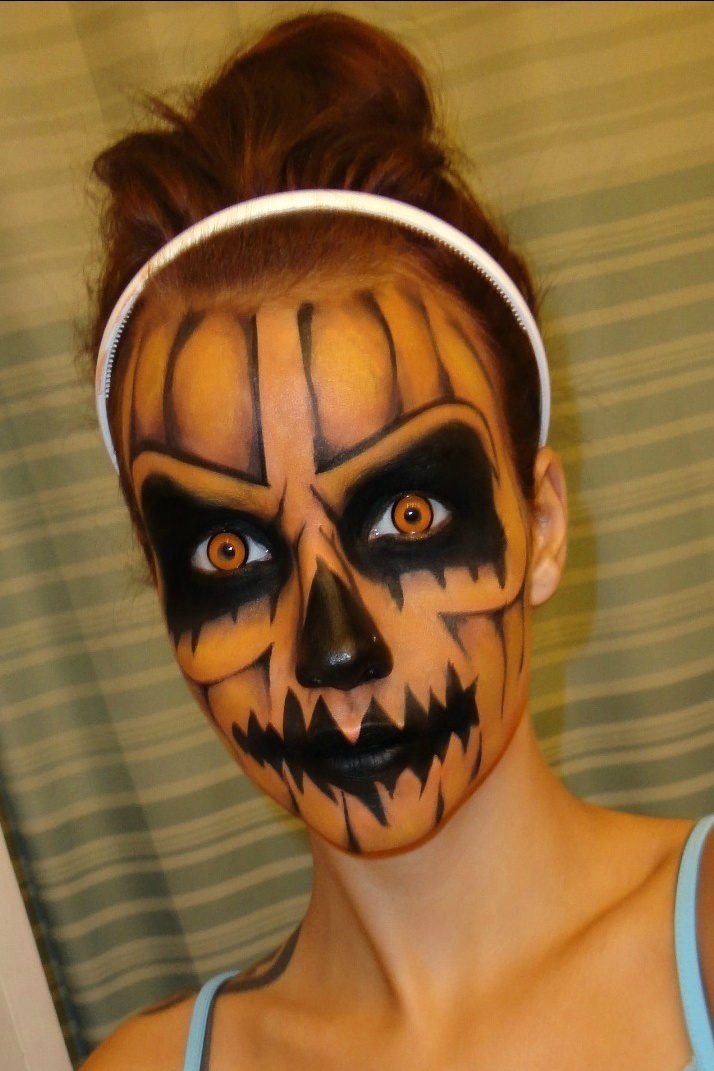
As I said before be careful and wear safety glasses, you don't want any of this stuff in your eyes. Also for those unfamiliar with using a Dremel tool when you cut through the metal sections of the printer body you will create a rain of sparks and small flakes of sharp metal. As such you should be wearing safety glasses or goggles during the cutting process and keep your hands away from the cutting disc. It's also the step where you need to pay attention to what you're doing as you could seriously injure yourself and/or ruin your printer modification completely. The next step is where you roll up your sleeves and start the cutting and modifying process. Once you have those three things removed we can start looking at the heart of modifying this printer, the lifting process. This tubing is necessary so make sure not to break it or remove it. You'll want to be careful here! This station simply pops out from the press fit connectors it's sitting on, but it will have a tubing system connected to it. Finally you'll want to remove the print head cleaning station. So to avoid this problem I simply removed the roller leaving a clear area for the circuit board to pass through. You don't really need all three sets and the center set could cause clearance issues when you send a circuit board through the printer. Next up is the pressure wheels in the center of the printer. Set this aside and we'll work more with it later. I'll talk more about how this system works later, but you'll want to remove that sensor from the back of the printer and unplug it from the circuit board. You'll need to relocate the paper feed sensor because the feeder no longer sends paper in from the top rear of the printer. Once you've gathered all of those things you're ready to begin.Īfter removing all the covers there are some parts that you should remove and set aside for later. A drill of some sort to attach the brackets Pliers or a socket wrench that fits the nuts or screws you'll be using A Dremel tool with grinding wheels to cut through metal An ink kit from (more details on this later)
HOW TO USE EPSON EASY PHOTO PRINT DRIVERS
The drivers for whichever printer and operating system you decide to use A small piece of scrap plywood and some other random scraps of 2x4 or something of the sort Some 4 - 40 screws (I used 1/2 inch long ones) Some type of brackets and screws to secure them with (I used 3, you'll see an image of them later on) Approximately 4 feet of 1/4 inch bent (90 degree corner piece) aluminum rail A sheet of aluminum or steel or some metal sheet (about 9 inches by 14.5 inches roughly) Obviously you'll need some form of an Epson inkjet printer probably of the C80 family as those are the ones I have seen modifications to in the past. So all that being said let's start with the tools and materials you'll need for this project: Hopefully this Instructable can serve as just that. I really tried to go into detail on everything I did in this process and the problems I had to troubleshoot because from looking around online there have been a few people who have done these modifications before, but no one really seems to have given a very good in-depth step by step build guide. Since I've been working on my own website ( I've documented everything about the project and thought it would be good to put it multiple places so hopefully numerous people can see it and try something new for themselves.
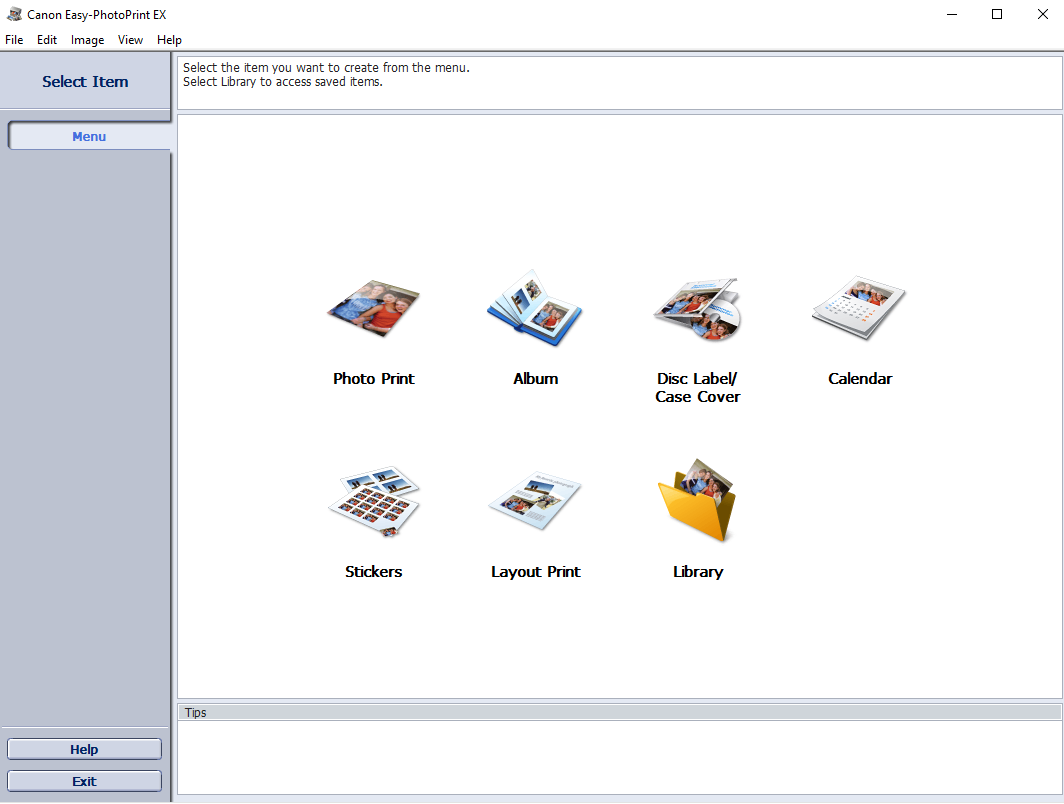
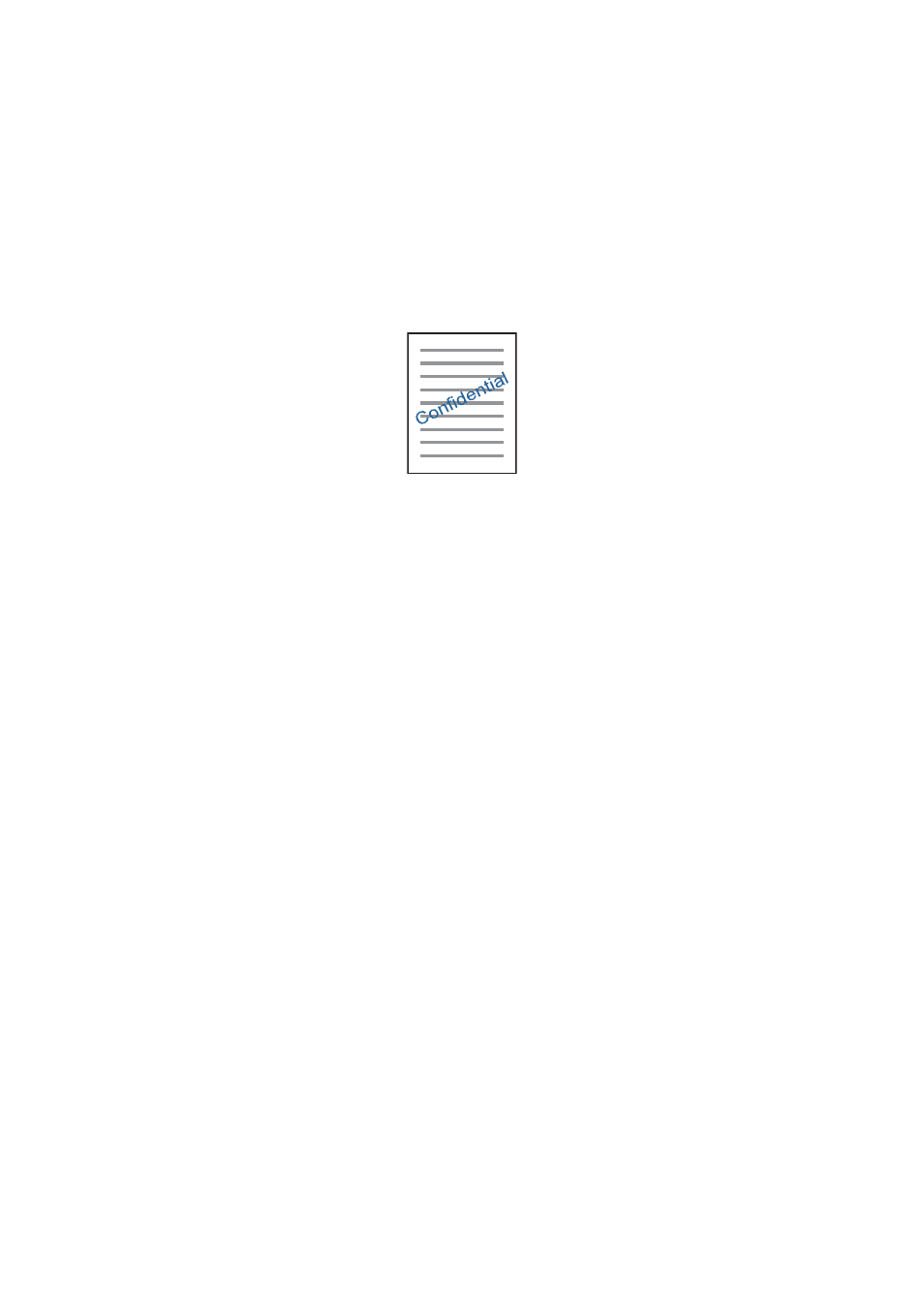
As you'll notice that webpage is centered around an Epson C84 printer, but Epson printers are all somewhat similar so I decided to try this method on the C86 I had lying around the house. This sentiment got me exploring new ideas for PCB creation which is the topic of this project.Ībout a year and a half ago I found this webpage on modifying an Epson inkjet printer into a printer capable of printing on thicker materials such as copper clad board used by hobbyists such as myself to create custom circuit boards. I’m not a fan of hit or miss I like to know something is going to work every time I try to do it. The specific pressure of the iron and timing both make it a hit or miss approach. While the toner transfer method has been my go to in the past it’s just not nearly as consistent as I would like it to be. I like being able to design something based on what I want in a circuit and just making it myself on the random weekend. Recently one of my focuses has been to find a way to make the PCB (Printed Circuit Board) creation process easier. SEE STEP 12 FOR NEW RESULTS AND AN ETCHING/PROJECT UPDATE!
